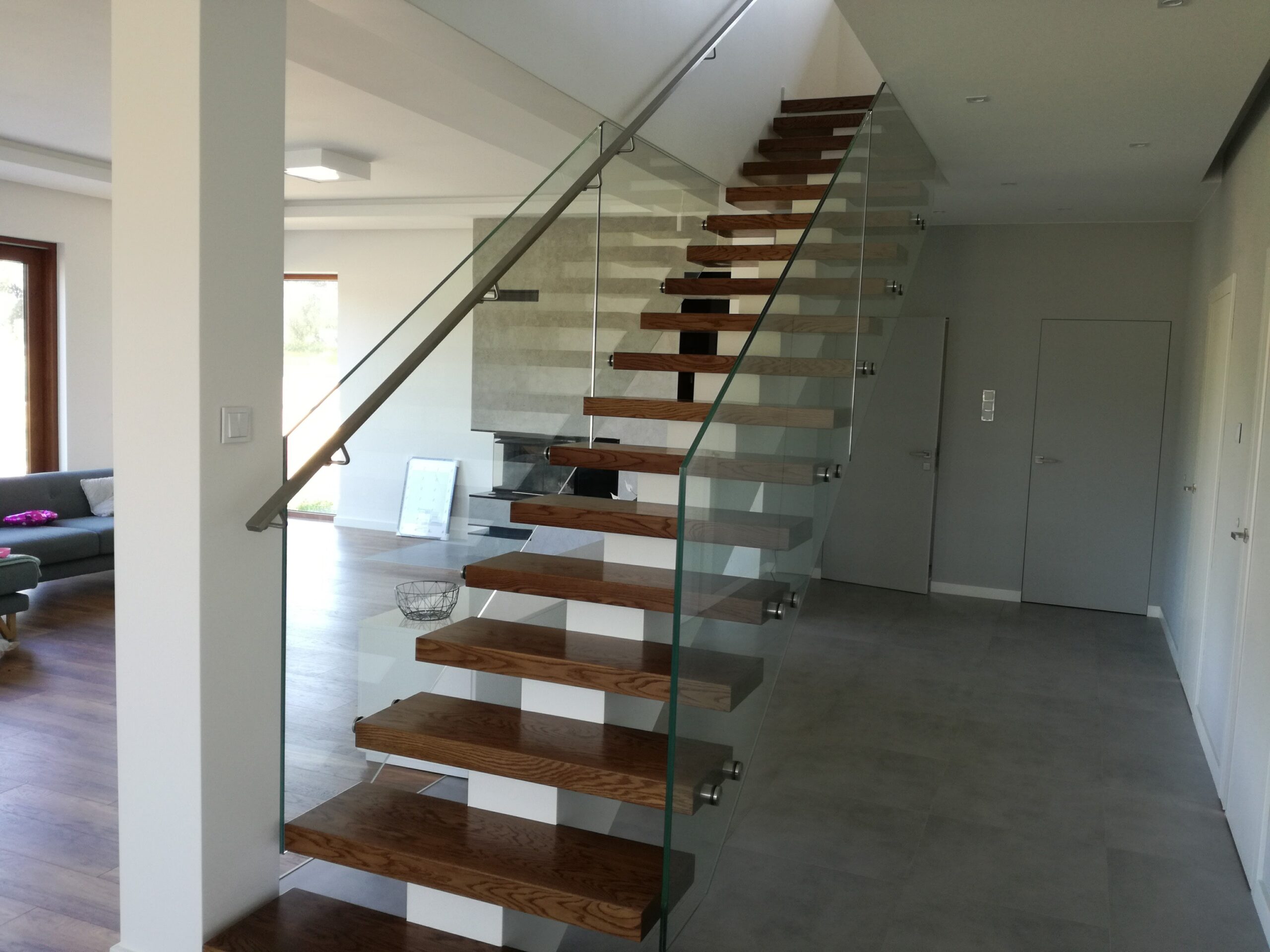
The topic may seem childishly simple, but is it really? To this day, no one in our beautiful country has seriously tackled this issue. We can draft (hastily) and pass laws, often in one day or maybe overnight… Okay, I’m exaggerating a bit, but doesn’t it bother you that there is no standard that clearly defines the type and thickness of glass depending on the type of railing? It may seem minor, but it has a significant impact on safety.
But let’s take it step by step
There are no simple answers without asking difficult questions. Everyone (hopefully) knows that the glass will be different if it’s used as a fill for a profile railing versus when it serves a structural/self-supporting role in a railing.
When and Where
VSG – Never 😊 and here opinions might differ from mine. I agree that in special cases, theoretically, such a laminate can be used, but… the mounting profiles must have the appropriate depth, the gaskets should fit well, and the glass surface should be small. I don’t know of such solutions myself, which, of course, doesn’t mean they don’t exist.
VSG/ESG – Here the topic broadens because the use of these types of laminates is extensive, and the main difference will be the thickness of the laminate, such as:
VSG/ESG 44.2 or VSG/ESG 44.4 can be used as infill for aluminum-glass, steel-glass railings, or showcases that can serve as railings. You need to ensure proper installation, meaning using mounting profiles with gaskets or point fasteners, although additional technical analysis is usually required here.
VSG/ESG 66.4 – This glass is used for both aluminum and steel railings, as well as self-supporting railings with one caveat: self-supporting railings with this type of laminate are designed for relatively low loads, usually not exceeding 0.5kN. Designing railings mounted linearly in profiles is different from those mounted at points.
VSG/ESG 88.8 – This laminate is widely used as a structural element in railings mounted both in linear profiles and at points. Nominal loads do not exceed 1kN. I wouldn’t be myself if I didn’t mention that for such loads, a handrail is necessary. This could be a channel glued on top of the glass or a handrail fastened with angular mounts.
VSG/ESG 10.10.4 – It’s getting real 😊. Using standard PVB or EVA films doesn’t change much in the design of self-supporting railings mounted linearly, but it does make a difference for point-mounted railings. You can definitely go for larger dimensions of individual panels or increase the horizontal spacing between mounts.
The situation changes when specialized inserts of 0.6 and 0.8mm thickness are used in the lamination process – this solution allows for designing railings with much higher strength. I have reviewed several test reports using these “magical” inserts, and they were so interesting that we started our own testing procedures for such laminates.
VSG/ESG 12.12.4 – Now we’re in a different league. Using this type of laminate with ordinary films can achieve up to 3kN, and with inserts even 5kN – although for such large loads, besides detailed glass analysis, a simulation or test of the entire mounting set and glass is necessary.
Wrapping Up
I know the topic is much broader than the brief case study described above. I didn’t want to bore you with the types of self-supporting profiles, point mounts and their contact surfaces, or the possibilities of using semi-tempered VSG/TVG laminates. I want you to understand the direction of selection. Remember, if the railings haven’t been tested by an accredited body, the absolute minimum is to conduct a computational model where both the glass and mounting elements are verified. Although nothing tells the truth like a pendulum test…
If you need more information, email me.
Łukasz Czarnecki